ડ્રાઈવર શાફ્ટ XCMG Liugong મોટર ગ્રેડર સ્પેરપાર્ટ્સ
ડ્રાઈવર શાફ્ટ
કારણ કે ત્યાં ઘણા પ્રકારના ફાજલ ભાગો છે, અમે તે બધાને વેબસાઇટ પર પ્રદર્શિત કરી શકતા નથી. કૃપા કરીને ચોક્કસ લોકો માટે અમારો સંપર્ક કરો.
ફાયદો
1. અમે તમારા માટે મૂળ અને આફ્ટરમાર્કેટ બંને ઉત્પાદનો સપ્લાય કરીએ છીએ
2. ઉત્પાદકથી સીધા ગ્રાહક સુધી, તમારી કિંમત બચાવો
3. સામાન્ય ભાગો માટે સ્થિર સ્ટોક
4. સ્પર્ધાત્મક શિપિંગ ખર્ચ સાથે, સમય ડિલિવરી સમયે
5. વ્યવસાયિક અને સેવા પછી સમયસર
પેકિંગ
કાર્ટન બોક્સ, અથવા ગ્રાહકોની વિનંતી અનુસાર.
વર્ણન
ડ્રાઇવર-શાફ્ટ બાંધકામ મશીનરી ચેસિસના ડ્રાઇવિંગ ભાગના મુખ્ય ભાગોમાંનું એક છે. તે જટિલ બેન્ડિંગ, ટોર્સનલ લોડ્સ અને ઉપયોગ દરમિયાન મોટા પ્રભાવના ભારને આધિન છે, જેના માટે અર્ધ-શાફ્ટને ઉચ્ચ થાક શક્તિ, કઠિનતા અને સારી વસ્ત્રો પ્રતિકારની જરૂર છે. અર્ધ-શાફ્ટની સેવા જીવન માત્ર ઉત્પાદન પ્રક્રિયાના ડિઝાઇન તબક્કે યોજના અને સામગ્રીની પસંદગીથી પ્રભાવિત નથી, પરંતુ ફોર્જિંગ ઉત્પાદન પ્રક્રિયા અને ફોર્જિંગનું ગુણવત્તા નિયંત્રણ પણ ખૂબ જ મહત્વપૂર્ણ છે.
ઉત્પાદન પ્રક્રિયામાં ગુણવત્તા વિશ્લેષણ અને નિયંત્રણનાં પગલાં
1 કાપવાની પ્રક્રિયા
બ્લેન્કિંગની ગુણવત્તા અનુગામી ફ્રી ફોર્જિંગ બ્લેન્ક્સની ગુણવત્તાને અસર કરશે અને ડાઇ ફોર્જિંગને પણ અસર કરશે. ખાલી કરવાની પ્રક્રિયામાં મુખ્ય ખામીઓ નીચે મુજબ છે.
1) લંબાઈ સહનશીલતા બહાર છે. બ્લેન્કિંગ લંબાઈ ખૂબ લાંબી અથવા ખૂબ ટૂંકી હોય છે, ખૂબ લાંબી ફોર્જિંગ કદમાં વધુ પડતી હકારાત્મક અને નકામી સામગ્રીનું કારણ બની શકે છે, અને ખૂબ ટૂંકા ફોર્જિંગને અસંતુષ્ટ અથવા નાના કદનું કારણ બની શકે છે. કારણ એ હોઈ શકે છે કે પોઝિશનિંગ બેફલ ખોટી રીતે સેટ કરવામાં આવી છે અથવા બ્લેન્કિંગ પ્રક્રિયા દરમિયાન પોઝિશનિંગ બેફલ ઢીલું અથવા અચોક્કસ છે.
2) અંતિમ ચહેરાની ઢાળ મોટી છે. વિશાળ અંત સપાટી ઢોળાવનો અર્થ છે કે રેખાંશ અક્ષના સંદર્ભમાં ખાલી જગ્યાની અંતિમ સપાટીનો ઝોક ઉલ્લેખિત સ્વીકાર્ય મૂલ્ય કરતાં વધી જાય છે. જ્યારે અંતિમ ચહેરાનો ઢોળાવ ખૂબ મોટો હોય છે, ત્યારે ફોર્જિંગ પ્રક્રિયા દરમિયાન ફોલ્ડ્સની રચના થઈ શકે છે. કારણ એ હોઈ શકે છે કે બ્લેન્કિંગ દરમિયાન બારને ક્લેમ્પ કરવામાં આવ્યો નથી, અથવા બેન્ડ સો બ્લેડની દાંતની ટોચ અસાધારણ રીતે પહેરવામાં આવી છે, અથવા બેન્ડ સો બ્લેડનું ટેન્શન ખૂબ નાનું છે, બેન્ડ સો મશીનની માર્ગદર્શિકા હાથ સમાન નથી. આડી રેખા, અને તેથી વધુ.
3) અંતિમ ચહેરા પર બર. બાર સામગ્રીને સોઇંગ કરતી વખતે, બરર્સ સામાન્ય રીતે અંતિમ વિરામ પર દેખાય છે. બર્ર્સ સાથેના બ્લેન્ક્સ જ્યારે ગરમ થાય ત્યારે સ્થાનિક ઓવરહિટીંગ અને ઓવરબર્નિંગનું કારણ બને છે અને ફોર્જિંગ દરમિયાન ફોલ્ડ અને ક્રેક કરવામાં સરળ હોય છે. એક કારણ એ છે કે કરવતની બ્લેડ વૃદ્ધ થઈ ગઈ છે, અથવા કરવતના દાંત પહેરેલા છે, પૂરતા તીક્ષ્ણ નથી, અથવા આરી બ્લેડના દાંત તૂટી ગયા છે; બીજું એ છે કે સો બ્લેડ લાઇનની ગતિ યોગ્ય રીતે સેટ કરેલી નથી. સામાન્ય રીતે, નવી આરી બ્લેડ ઝડપી હોઈ શકે છે, અને જૂની આરી બ્લેડ ધીમી છે.
4) અંતના ચહેરા પર તિરાડો. જ્યારે સામગ્રીની કઠિનતા અસમાન હોય છે અને સામગ્રીનું વિભાજન ગંભીર હોય છે, ત્યારે અંતિમ ચહેરા પર તિરાડો ઉત્પન્ન કરવી સરળ છે. અંતમાં તિરાડો સાથે બ્લેન્ક્સ માટે, ફોર્જિંગ દરમિયાન તિરાડો વધુ વિસ્તરશે.
બ્લેન્કિંગની ગુણવત્તા સુનિશ્ચિત કરવા માટે, ઉત્પાદન પ્રક્રિયા દરમિયાન નીચેના નિવારક નિયંત્રણ પગલાં લેવામાં આવ્યા છે: બ્લેન્કિંગ પહેલાં, પ્રક્રિયાના નિયમો અને પ્રક્રિયા કાર્ડ્સ અનુસાર સામગ્રીની બ્રાન્ડ, સ્પષ્ટીકરણ, જથ્થો અને સ્મેલ્ટિંગ ફર્નેસ (બેચ) નંબરની ચકાસણી કરો. . અને રાઉન્ડ સ્ટીલ બારની સપાટીની ગુણવત્તા તપાસો; ફોર્જિંગ નંબર, મટિરિયલ બ્રાન્ડ, સ્પેસિફિકેશન અને મેલ્ટિંગ ફર્નેસ (બેચ) નંબર અનુસાર બ્લેન્કિંગ બેચમાં કરવામાં આવે છે, અને બ્લેન્ક્સની સંખ્યા વિદેશી સામગ્રીના મિશ્રણને રોકવા માટે પરિભ્રમણ ટ્રેકિંગ કાર્ડ પર સૂચવવામાં આવે છે; સામગ્રીને કાપતી વખતે, "પ્રથમ નિરીક્ષણ", "સ્વ-નિરીક્ષણ" અને "પેટ્રોલ નિરીક્ષણ" ની સિસ્ટમ સખત રીતે અમલમાં મૂકવી જોઈએ. પરિમાણીય સહિષ્ણુતા, અંતિમ ઢોળાવ અને ખાલી જગ્યાના છેડાની પ્રક્રિયાની આવશ્યકતાઓ અનુસાર વારંવાર તપાસ કરવી જોઈએ, અને નિરીક્ષણ યોગ્ય છે અને ઉત્પાદનની સ્થિતિ ચિહ્નિત થયેલ છે. ઓર્ડર પછીથી બદલી શકાય છે; બ્લેન્કિંગ પ્રક્રિયા દરમિયાન, જો બ્લેન્ક્સમાં ફોલ્ડ, ડાઘ, અંતમાં તિરાડો અને અન્ય દૃશ્યમાન ખામીઓ જોવા મળે, તો સમયસર નિકાલ માટે નિરીક્ષક અથવા ટેકનિશિયનને જાણ કરવી જોઈએ; બ્લેન્કિંગ સાઇટને સ્વચ્છ રાખવી જોઈએ, વિવિધ સામગ્રીના ગ્રેડ અને સ્મેલ્ટિંગ ફર્નેસ (બેચ) નંબર, વિશિષ્ટતાઓ અને પરિમાણો અલગથી મૂકવા જોઈએ અને મિશ્રણ ટાળવા માટે સ્પષ્ટ રીતે ચિહ્નિત કરવું જોઈએ. જો સામગ્રીની અવેજીની આવશ્યકતા હોય, તો સામગ્રીના અવેજીકરણ માટેની મંજૂરી પ્રક્રિયાઓનું સખતપણે પાલન કરવું આવશ્યક છે, અને મંજૂરી પછી જ સામગ્રીને છૂટા કરી શકાય છે.
2 હીટિંગ પ્રક્રિયા.
અર્ધ-શાફ્ટ ઉત્પાદન પ્રક્રિયાને બે આગ દ્વારા ગરમ કરવામાં આવે છે, ફ્રી ફોર્જિંગ બિલેટને ગેસ ભઠ્ઠી દ્વારા ગરમ કરવામાં આવે છે, અને ડાઇ ફોર્જિંગને ઇન્ડક્શન ઇલેક્ટ્રિક ફર્નેસ દ્વારા ગરમ કરવામાં આવે છે, તેથી હીટિંગ ક્રમનું નિવારક નિયંત્રણ વધુ જટિલ અને વધુ મુશ્કેલ છે; હીટિંગ ગુણવત્તા સુનિશ્ચિત કરવા માટે, અમે નીચેની ગુણવત્તા સ્પષ્ટીકરણો ઘડી છે:
જ્યારે ગેસ સ્ટોવને ગરમ કરવામાં આવે છે, ત્યારે તેને ઉચ્ચ તાપમાનના ઝોનમાં સામગ્રીને સીધી ચાર્જ કરવાની મંજૂરી નથી, અને તેને ખાલી જગ્યાની સપાટી પર સીધી જ્યોતને છાંટવાની મંજૂરી નથી; ઇલેક્ટ્રિક ફર્નેસમાં ગરમ કરતી વખતે, ખાલી જગ્યાની સપાટી તેલથી દૂષિત થવી જોઈએ નહીં. હીટિંગ સ્પેસિફિકેશન્સ અનુરૂપ ફોર્જિંગ પ્રક્રિયાના નિયમોની જરૂરિયાતો અનુસાર લાગુ કરવામાં આવશે, અને હીટિંગ પરિમાણો સ્થિર અને વિશ્વસનીય છે તે સાબિત કરવા માટે શિફ્ટ પહેલાં બ્લેન્ક્સના 5-10 ટુકડાઓનું હીટિંગ તાપમાન સંપૂર્ણ રીતે ચકાસવામાં આવશે. સાધનસામગ્રી અને ટૂલિંગ સમસ્યાઓને કારણે સમયસર બિલેટ બનાવટી કરી શકાતી નથી. તેને ઠંડક દ્વારા અથવા ભઠ્ઠીમાંથી બહાર કાઢીને પ્રક્રિયા કરી શકાય છે. દબાણ કરાયેલ બિલેટને અલગથી ચિહ્નિત અને સંગ્રહિત કરવું જોઈએ; બિલેટને વારંવાર ગરમ કરી શકાય છે, પરંતુ હીટિંગની સંખ્યા 3 ગણી વધી શકતી નથી. જ્યારે ખાલી જગ્યાને ગરમ કરવામાં આવે ત્યારે સામગ્રીના તાપમાનનું વાસ્તવિક સમયમાં અથવા નિયમિતપણે ઇન્ફ્રારેડ થર્મોમીટર વડે નિરીક્ષણ કરવું જોઈએ, અને હીટિંગ રેકોર્ડ બનાવવો જોઈએ.
3 બિલેટ બનાવવાની પ્રક્રિયા.
બિલેટ બનાવતી વખતે સામાન્ય ખામીઓમાં મધ્યવર્તી બિલેટ સળિયાનો વધુ પડતો વ્યાસ અથવા લંબાઈ, સપાટી પરના હથોડાના નિશાન અને નબળા સ્ટેપ ટ્રાન્ઝિશનનો સમાવેશ થાય છે. જો સળિયાનો વ્યાસ ખૂબ સકારાત્મક હોય, તો તેને ડાઇ ફોર્જિંગ દરમિયાન પોલાણમાં મૂકવું મુશ્કેલ બનશે. જો સળિયો નાનો નેગેટિવ હોય, તો ફોર્જિંગની કોક્સિએલિટી ખૂબ નબળી હોઈ શકે છે કારણ કે ડાઈ ફોર્જિંગ દરમિયાન સળિયાના મોટા ગેપને કારણે; સપાટી પરના હથોડાના નિશાન અને નબળા પગલાનું સંક્રમણ શક્ય છે અંતિમ ફોર્જિંગની સપાટી પર ખાડાઓ અથવા ફોલ્ડ્સ તરફ દોરી જાય છે.
4 ડાઇ ફોર્જિંગ અને ટ્રિમિંગ પ્રક્રિયા.
સેમી-શાફ્ટ ડાઇ ફોર્જિંગ પ્રક્રિયામાં મુખ્ય ખામીઓમાં ફોલ્ડિંગ, અપૂરતું ફિલિંગ, અંડરપ્રેશર (હિટિંગ નહીં), મિસલાઈનમેન્ટ વગેરેનો સમાવેશ થાય છે.
1) ફોલ્ડ. અર્ધ-શાફ્ટનું ફોલ્ડિંગ ફ્લેંજના અંતિમ ચહેરા પર અથવા સ્ટેપ ફિલેટમાં અથવા ફ્લેંજની મધ્યમાં સામાન્ય છે, અને સામાન્ય રીતે ચાપ આકારનું અથવા તો અર્ધ-ગોળાકાર પણ હોય છે. ફોલ્ડની રચના ખાલી અથવા મધ્યવર્તી ખાલીની ગુણવત્તા, ઘાટની ડિઝાઇન, ઉત્પાદન અને લ્યુબ્રિકેશન, ઘાટ અને હથોડીને બાંધવા અને ફોર્જિંગની વાસ્તવિક કામગીરી સાથે સંબંધિત છે. ફોલ્ડિંગ સામાન્ય રીતે નરી આંખે જોઈ શકાય છે જ્યારે ફોર્જિંગ લાલ ગરમ સ્થિતિમાં હોય છે, પરંતુ તે સામાન્ય રીતે પછીના તબક્કામાં ચુંબકીય કણોનું નિરીક્ષણ પસાર કરી શકે છે.
2) આંશિક રીતે અસંતોષથી ભરેલું. અર્ધ-શાફ્ટ ફોર્જિંગનો આંશિક અસંતોષ મુખ્યત્વે સળિયા અથવા ફ્લેંજના બાહ્ય ગોળાકાર ખૂણાઓ પર થાય છે, જે ગોળાકાર ખૂણા ખૂબ મોટા હોવાથી અથવા કદ જરૂરિયાતોને પૂર્ણ કરતા નથી તે રીતે પ્રગટ થાય છે. અસંતોષ ફોર્જિંગના મશીનિંગ ભથ્થામાં ઘટાડો તરફ દોરી જશે, અને જ્યારે તે ગંભીર હશે, ત્યારે પ્રક્રિયાને રદ કરવામાં આવશે. અસંતોષના કારણો આ હોઈ શકે છે: મધ્યવર્તી બિલેટ અથવા ખાલી જગ્યાની ડિઝાઇન ગેરવાજબી છે, તેનો વ્યાસ અથવા લંબાઈ અયોગ્ય છે; ફોર્જિંગ તાપમાન ઓછું છે, અને ધાતુની પ્રવાહીતા નબળી છે; ફોર્જિંગ ડાઇનું લુબ્રિકેશન અપૂરતું છે; ડાઇ કેવિટીમાં ઓક્સાઇડ સ્કેલનું સંચય, વગેરે.
3) મિસપ્લેસમેન્ટ. મિસલાઈનમેન્ટ એ ફોર્જિંગના ઉપરના અડધા ભાગનું વિસ્થાપન છે જે વિભાજનની સપાટી સાથે નીચલા અડધા ભાગની તુલનામાં છે. મિસપ્લેસમેન્ટ મશીનિંગ સ્થિતિને અસર કરશે, પરિણામે અપૂરતું સ્થાનિક મશીનિંગ ભથ્થું. કારણો હોઈ શકે છે: હેમર હેડ અને માર્ગદર્શિકા રેલ વચ્ચેનું અંતર ખૂબ મોટું છે; ફોર્જિંગ ડાઇ લોક ગેપની ડિઝાઇન ગેરવાજબી છે; મોલ્ડ ઇન્સ્ટોલેશન સારું નથી.
5 ટ્રિમિંગ પ્રક્રિયા.
ટ્રિમિંગ પ્રક્રિયામાં મુખ્ય ગુણવત્તાની ખામી મોટી અથવા અસમાન શેષ ફ્લેશ છે. મોટી અથવા અસમાન શેષ ફ્લેશ મશીનિંગ સ્થિતિ અને ક્લેમ્પિંગને અસર કરી શકે છે. સ્થાનિક મશીનિંગ ભથ્થામાં વધારા ઉપરાંત, તે મશીનિંગ વિચલનનું કારણ બનશે, અને તૂટક તૂટક કટીંગને કારણે કટીંગ પણ થઈ શકે છે. કારણ આ હોઈ શકે છે: ટ્રિમિંગ ડાઇનો પંચ, ડાઇનો ગેપ યોગ્ય રીતે ડિઝાઇન કરવામાં આવ્યો નથી, અથવા ડાઇ પહેરેલ અને વૃદ્ધ છે
ઉપરોક્ત ખામીઓને રોકવા અને ફોર્જિંગની ગુણવત્તા સુનિશ્ચિત કરવા માટે, અમે નિવારણ અને નિયંત્રણના પગલાંની શ્રેણી ઘડી અને અપનાવી છે: ડિઝાઇન સમીક્ષા અને પ્રક્રિયાની ચકાસણી દ્વારા યોગ્ય ખાલી અથવા મધ્યવર્તી ખાલી કદ નક્કી કરો; મોલ્ડ ડિઝાઇન અને વેરિફિકેશન સ્ટેજમાં, પરંપરાગત મોલ્ડ સિવાય કેવિટી લેઆઉટ, બ્રિજ અને સિલો ડિઝાઇન ઉપરાંત, ફોલ્ડિંગ અને મિસ-શિફ્ટિંગને રોકવા માટે સ્ટેપ ફિલેટ્સ અને લોક ગેપ્સ પર વિશેષ ધ્યાન આપવામાં આવ્યું છે, પ્રક્રિયાનું કડક ગુણવત્તા નિયંત્રણ. બ્લેન્કિંગ, હીટિંગ અને ફ્રી ફોર્જિંગ બિલેટ, અને બિલેટની ત્રાંસી સપાટી પર ધ્યાન કેન્દ્રિત કરો. અંતિમ ચહેરા પર ડિગ્રી અને બરર્સ, મધ્યવર્તી બિલેટનું પગલું સંક્રમણ, સળિયાની લંબાઈ અને સામગ્રીનું તાપમાન.
આપણું-વેરહાઉસ1
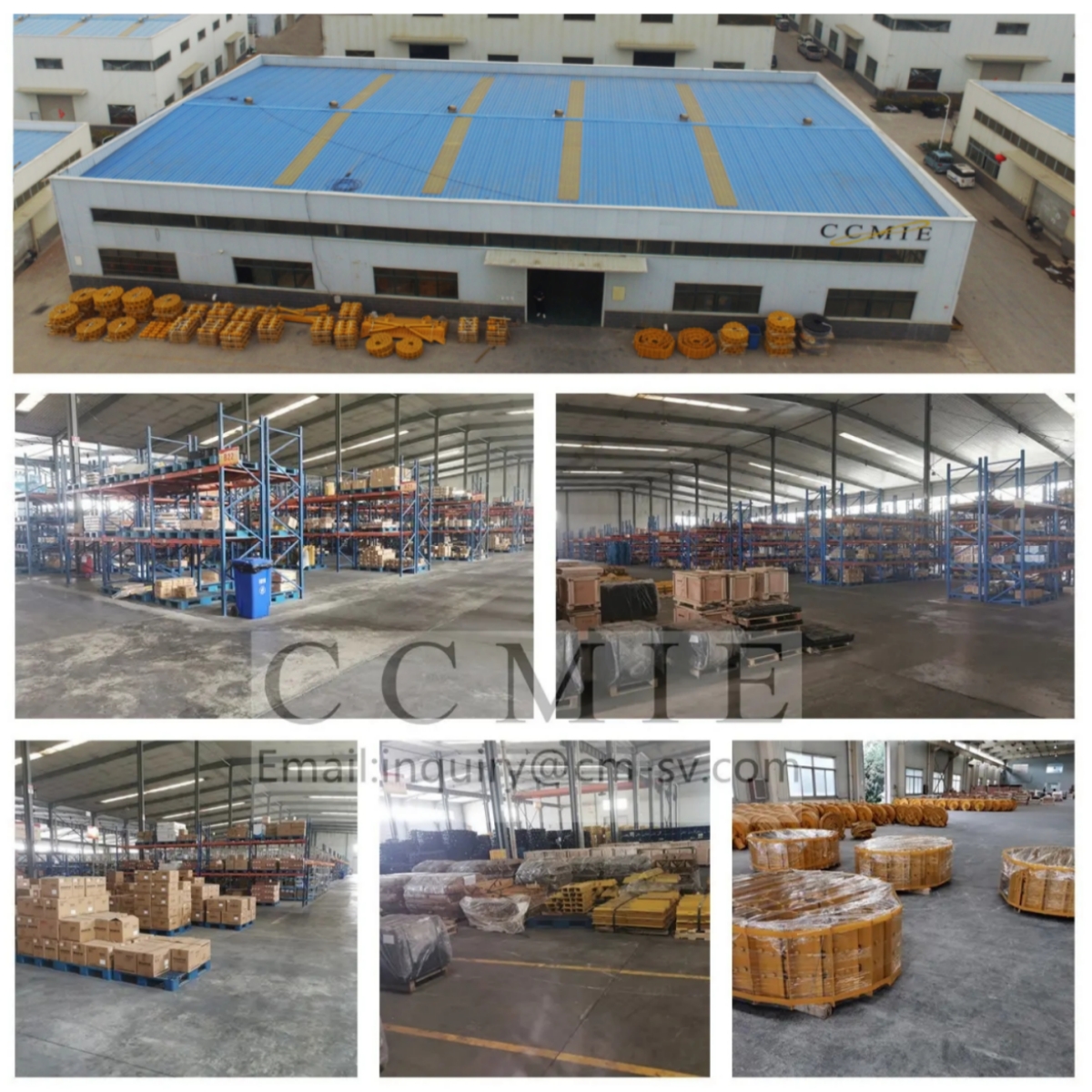
પેક અને જહાજ

- એરિયલ બૂમ લિફ્ટ
- ચાઇના ડમ્પ ટ્રક
- કોલ્ડ રિસાયકલર
- શંકુ કોલું લાઇનર
- કન્ટેનર સાઇડ લિફ્ટર
- દાદી બુલડોઝર ભાગ
- ફોર્કલિફ્ટ સ્વીપર જોડાણ
- Hbxg બુલડોઝર ભાગો
- Howo એન્જિન ભાગો
- હ્યુન્ડાઇ ઉત્ખનન હાઇડ્રોલિક પંપ
- કોમાત્સુ બુલડોઝર ભાગો
- કોમાત્સુ ઉત્ખનન ગિયર શાફ્ટ
- Komatsu Pc300-7 ઉત્ખનન હાઇડ્રોલિક પંપ
- Liugong બુલડોઝર ભાગો
- સેની કોંક્રિટ પંપના સ્પેર પાર્ટ્સ
- સેની એક્સેવેટર સ્પેર પાર્ટ્સ
- Shacman એન્જિન ભાગો
- શાંતુઇ બુલડોઝર ક્લચ શાફ્ટ
- શાન્તુઇ બુલડોઝર કનેક્ટિંગ શાફ્ટ પિન
- શાંતુઇ બુલડોઝર નિયંત્રણ લવચીક શાફ્ટ
- શાંતુઇ બુલડોઝર લવચીક શાફ્ટ
- શાંતુઇ બુલડોઝર લિફ્ટિંગ સિલિન્ડર રિપેર કિટ
- શાંતુઇ બુલડોઝર ભાગો
- શાંતુઇ બુલડોઝર રીલ શાફ્ટ
- શાંતુઇ બુલડોઝર રિવર્સ ગિયર શાફ્ટ
- Shantui બુલડોઝર સ્પેરપાર્ટ્સ
- શાંતુઇ બુલડોઝર વિંચ ડ્રાઇવ શાફ્ટ
- શાંતુઇ ડોઝર બોલ્ટ
- શાંતુઇ ડોઝર ફ્રન્ટ આઈડલર
- શાંતુઇ ડોઝર ટિલ્ટ સિલિન્ડર રિપેર કિટ
- Shantui Sd16 બેવલ ગિયર
- Shantui Sd16 બ્રેક લાઇનિંગ
- Shantui Sd16 ડોર એસેમ્બલી
- Shantui Sd16 O-રિંગ
- Shantui Sd16 ટ્રેક રોલર
- Shantui Sd22 બેરિંગ સ્લીવ
- Shantui Sd22 ઘર્ષણ ડિસ્ક
- Shantui Sd32 ટ્રેક રોલર
- Sinotruk એન્જિન ભાગો
- વાહન ખેંચવાની ટ્રક
- Xcmg બુલડોઝર ભાગો
- Xcmg બુલડોઝર સ્પેર પાર્ટ્સ
- Xcmg હાઇડ્રોલિક લોક
- Xcmg ટ્રાન્સમિશન
- Yuchai એન્જિન ભાગો